1er Congreso Universal de las Ciencias y la Investigación
← vista completaPublicado el 1 de septiembre de 2022 | http://doi.org/10.5867/medwave.2022.S2.UTA187
Plataforma de reconfiguración dinámica de control automático de un proceso industrial basado en IEC-61499 y multiagentes.
Dynamic reconfiguration platform for automatic control of an industrial process based on IEC-61499 and multi-agents.
Resumen
Introducción The constant increase in the hardware elements that be part of an automation system for industrial control and its greater complexity in the design of systems make that current industrial control methods adapt to new scenarios that are shown today and in the future, which has allowed the development of models more robust and adaptable controls to any environment or situation (Bonci et al., 2019). To answer to all these new demands of intelligent manufacturing, industrial automation systems must support reconfigurable, modular, and scalable systems, if possible dynamically. Current automated systems with a centralized feature lack these qualities, which is why they lose efficiency and new control alternatives are increasingly being chosen (Ribeiro & Bjorkman, 2018). The aim of the project is to test the feasibility of collaborative development of automation applications following the dynamic reconfiguration of systems based on multi-agent (MAS). The interoperability provisions developed by the standardization working group of the Open Process Automation Forum (OPAF) are used. The use of function blocks that will be developed as part of the OPAF standards will facilitate the interchangeability and interoperability of the industrial automation system. The IEC 61499 standard will be used as the integration standard between monitoring and automation with dynamic reconfiguration. This proposed is to ensure that downtime is minimal in the event of a stoppage due to disconnection in any industrial process, and that, furthermore, once the process has been recovered, it can be resumed from the point where it failed.
Objetivos Develop a Multi-agent system based on the IEC 61499 standard that allows dynamic reconfiguration in the FESTO MPS 500 Distributing station for continuous operation of the process in the event of an error or failure.
Método This research uses an architecture based on the IEC 61499 standard, which seeks to separate sensors, actuators, and control into sub-applications; while the control is assembled by a multi-agent system (MAS) that communicates with each other through XMPP (Extensible Messaging and Presence Communication Protocol).
Principales resultados A multi-agent hardware and software system based on the IEC 61499 standard that allows dynamic reconfiguration in the FESTO MPS 500 Distributing station for continuous operation of the process in the event of an error or failure
Conclusiones When a fault occurs due to disconnection or the controller is damaged in industrial processes, the open platform for dynamic reconfiguration detects it and another control hardware device takes the control at the point where this fault was detected, allowing production downtime to be reduced.
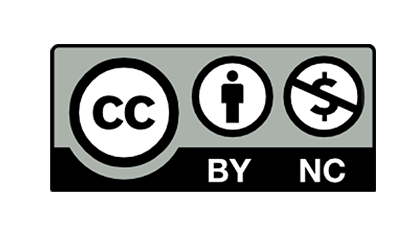